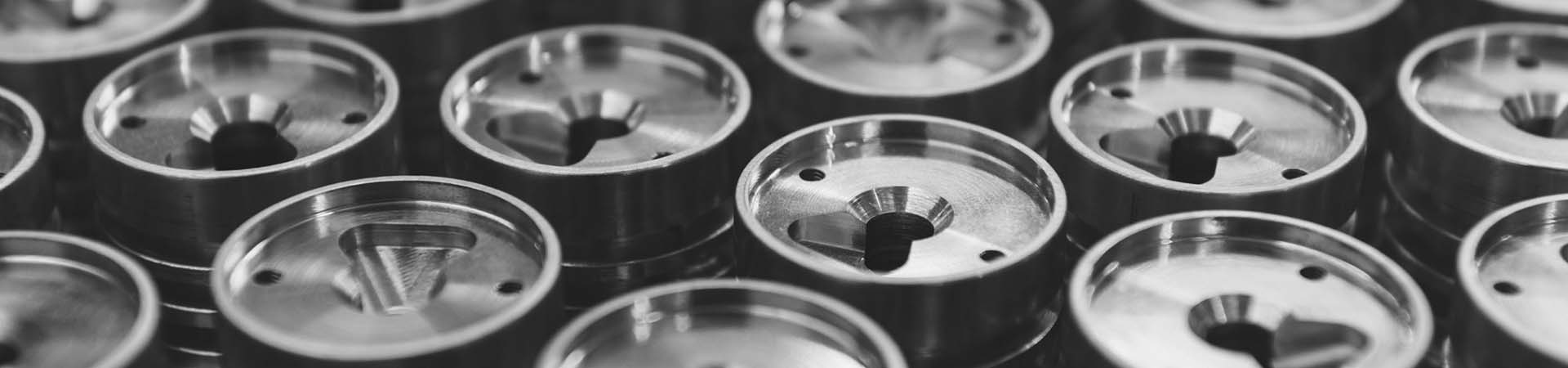
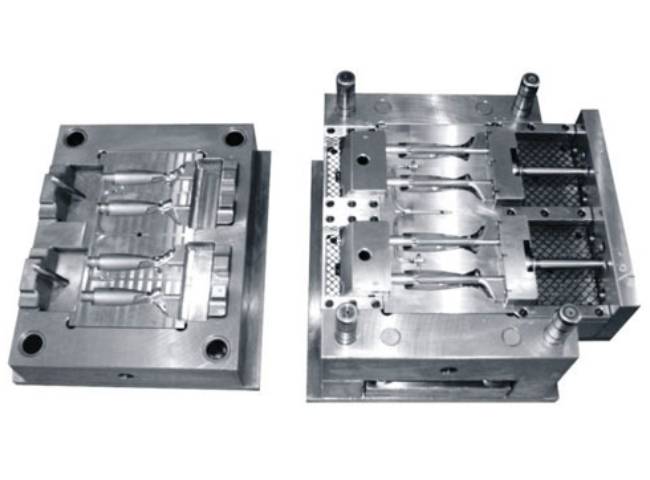
Die casting
In the process of die casting, molten metal is forced into a mold cavity under high pressure to make durable and stable metal parts. Die casting is also one of the fastest methods to make tools and parts by converting molten liquid metal into a re-usable prototype. The products are finished by coloring them using powder coating.
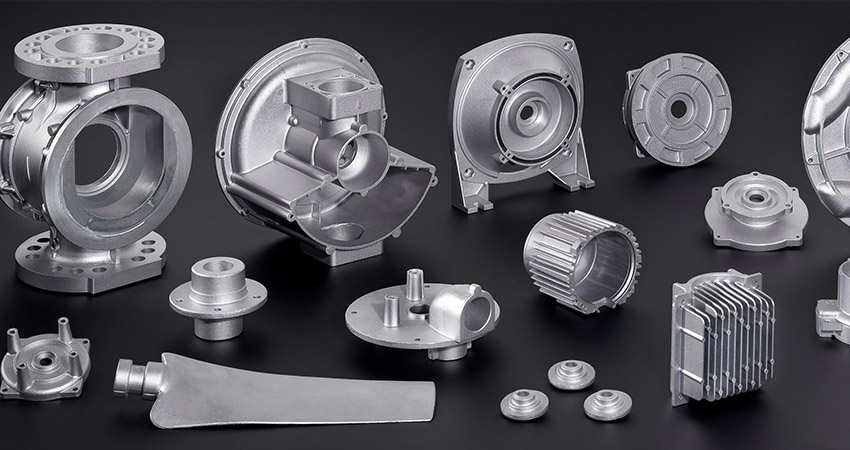
Precision
Small products or tools can be manufactured using die casting. Die casting produces prototypes of similar dimensions, maintaining precision every time. Products made through die casting maintain stability dimensionally and are highly tolerant of many factors. An experienced die caster can help in reducing the costs of casting.
Fast
Die casting is so far the fastest process of creating non-ferrous metallic parts precisely. The injected molten metal into the die cavity solidifies quickly. The manufacturing time depends on the product type, the material used, the complexity of the structure. Though the equipment required and dies are expensive, we try our best to cut the costs wherever possible.
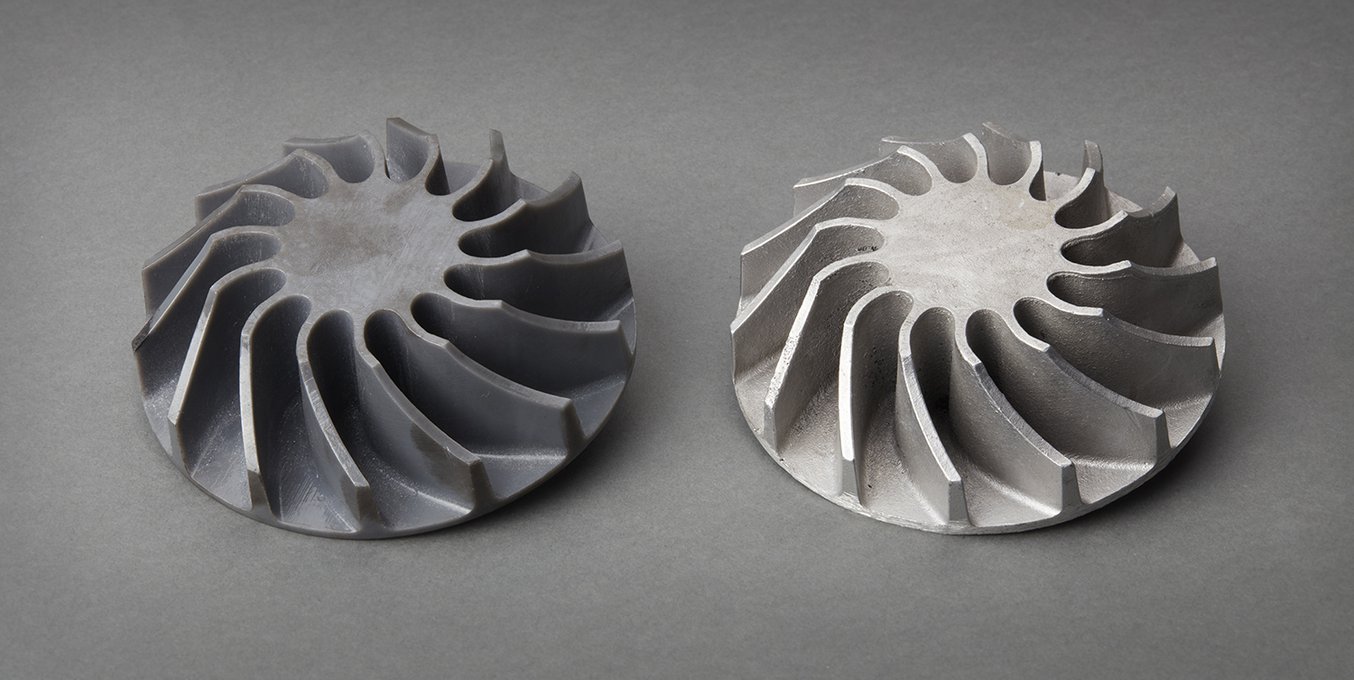
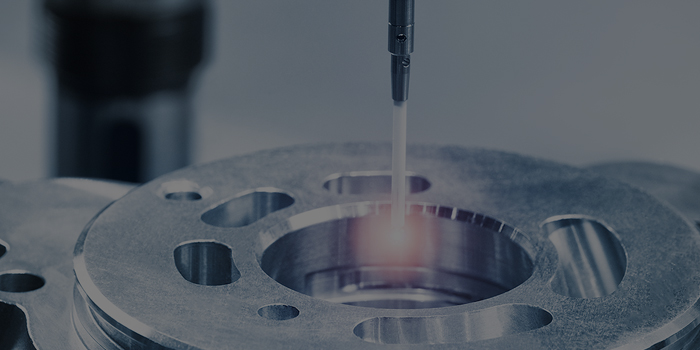
Durable
Products made from die casting are usually hard when compared to products made by injection molding. Die casting creates robust and efficient products, though the model is complicated. The products also heat resistant. The finishing process of the products is also quick and easy, holes (if required) can be bored, surfaces can be polished.